Bar & Restaurant Equipment
Multi-Flow offers a full range of Bar & Restaurant equipment to help you succeed in demanding bar services and commercial kitchens. We offer a full range of equipment options that include; bar and beer equipment, all types of soda and beverage dispensing systems, frozen beverage equipment, ice machines and ice bins, single and double door walk-in coolers, reach-in bottle coolers, along with kitchen and cooking equipment. We offer equipment rental programs and the sales of new and used equipment to help you in any possible manner to best equip your bar or restaurant. We offer all major name brands of equipment you are familiar with, and we install and service all the equipment we offer.
The Range of Equipment We Offer
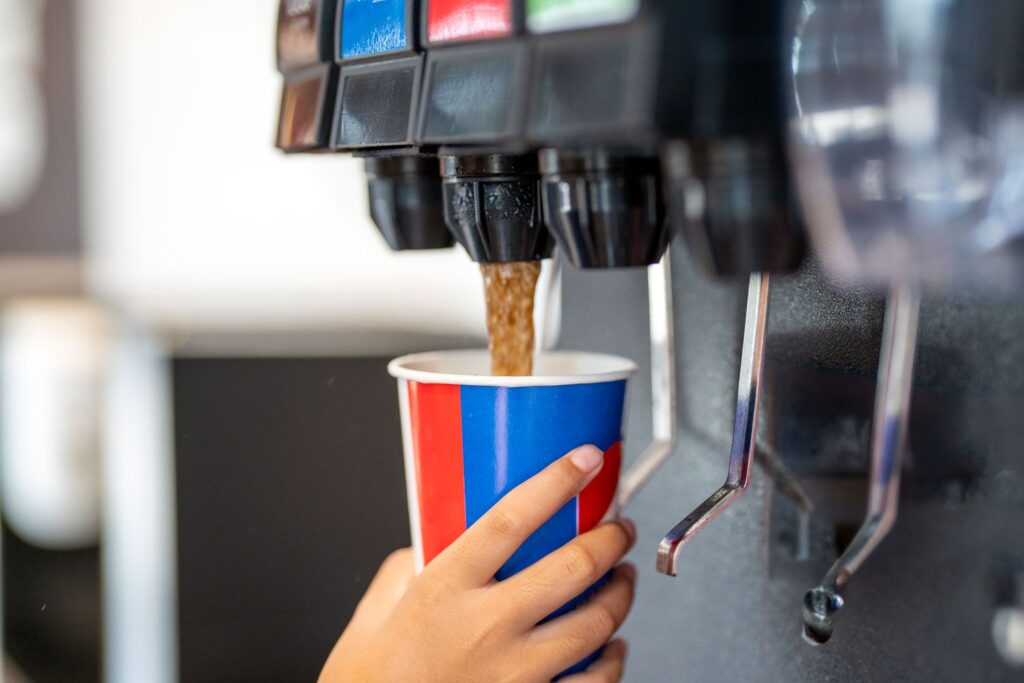
Beverage Dispensers
• Soda Bar Guns
• Fountain Dispensers
• Juice / Coffee Dispensers
• Bag-In-Box Rack System
• Spray Dispensers
• Chiller Systems
• Jet Spray Dispensers
• Tea Urn
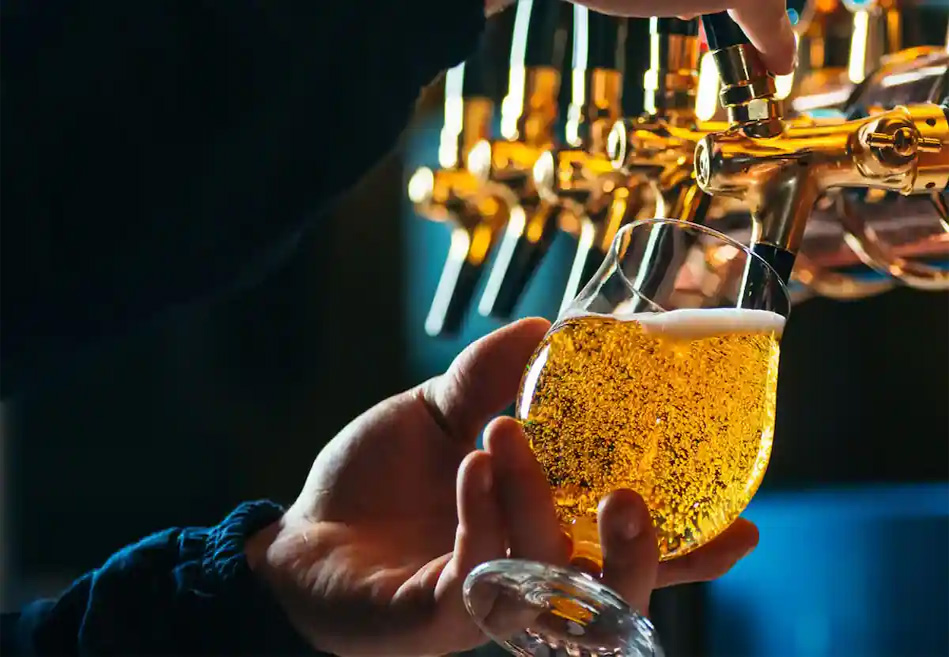
Draft Beer Systems
• Full Glycol Systems
• Air-Chute Systems
• Direct Draw Units (DDU)
• CO2 Blenders
• Nitrogen Generators
• Manual and Electronic Beer Line Cleaning
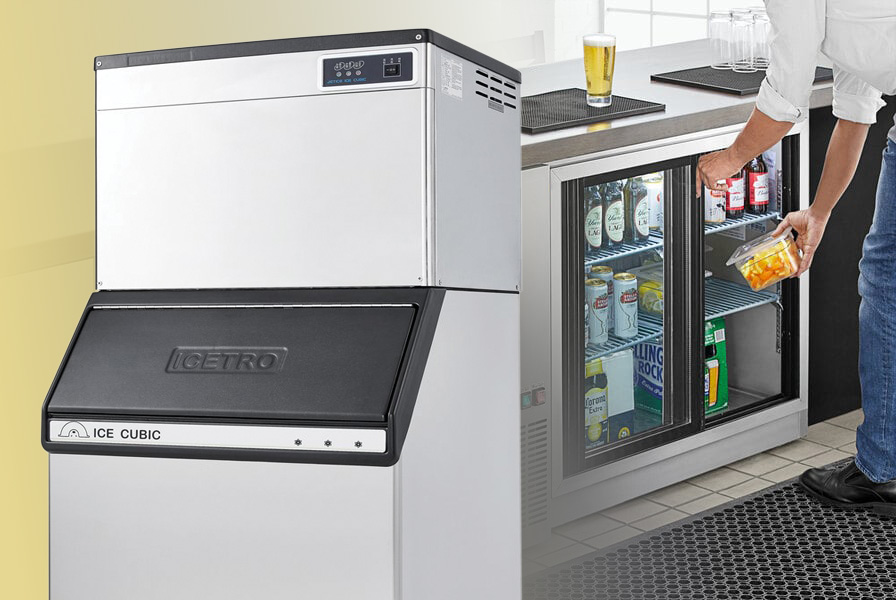
Ice Machines / Refrigeration
• Full Cube Ice Machines
• Half Cube Ice Machines
• Frozen Beverage Equipment
• Back Bar Coolers
• Reach-In Bottle Coolers
• Walk-In Coolers
At Multi-Flow Service is Priority #1
Multi-Flow takes great pride in our reliable route delivery system enabled by our team of Customer Service Technicians. Multi-Flow is there when you need us 7 days a week, including all holidays. Multi-Flow’s phones are staffed 7 days a week, by our courteous customer service representatives for your peace of mind and convenience.
Each of Multi-Flow’s customers are assigned a professional Customer Service technician who not only delivers your product needs but is trained to handle all basic service needs of your equipment while they are on site and completes a preventive maintenance check with every visit and delivery
Multi-Flow’s Service Program Includes the Following:
Multi-Flow has installation specialists to professionally install any equipment it rents or sells (new and used sales) and we provide the following :
• All the necessary equipment for the dispensing of soft drinks, juices and beverages
• Dispensing Equipment repair and/or replacement as required.
• Beer systems, Ice Machines, Margarita and Slushie units’ sales and service
• Preventive Maintenance Programs
• Once installed Multi-Flow technicians will clean, maintain, and repair our equipment as needed, giving you peace of mind..
Preventative Maintenance Programs for Ice Machines
– Which May Be Applied to All the Equipment We Supply –
An “ounce of prevention is worth a pound of cure” hence the saying implying how preventative maintenance is a practice we should all do to prolong the life of our equipment. Ice machines, refrigerators, coolers and other restaurant equipment require periodic maintenance to assure maximum performance and efficiency. To keep the overall operating cost down and efficiency up, regular preventative maintenance must be performed. Detailed portions as well as an annual or semi-annual cleaning and inspection should be done by our qualified service technicians with ice machine and equipment experience. In some areas where harsh water conditions exist it may be necessary to have the unit professionally cleaned more often than once a year. The installation of a properly sized water filtration or treatment system will reduce scale build up in the ice machine. We highlight below both the procedures and benefits for maintaining your equipment.
Quarterly
Procedure:
We turn off water supply and remove water supply pipe fitting from the water valve. Inspect and clean the water valve inlet screen. Wipe out the reservoir with a neutral cleaner and rinse thoroughly. Check the evaporator for calcium and lime deposits. Check the interior of the unit for unusual oil spots and water drips. Investigate any unusual findings and address them before a problem occurs.
Benefits:
Keeps ice clean and tasting fresh by removing scale and bacteria from bin. Provides consistent ice quality. Ensures proper water flow to the ice machine, reduces cleaning time spent during annual professional cleanings. Keeps the machine performing at maximum production and efficiency.
Semi-Annual
Procedure:
On remote condensers, we check for a dirty or clogged condenser coil. Replace external water filters if not done so at earlier intervals. At this time, you may want to have a qualified service technician to perform a professional cleaning and unit inspection.
Benefits:
Maximum efficiency of equipment, proper production and quality of ice, lower operating cost and early detection of problems that could cause major failures resulting in equipment down time.
Annually
Procedure:
All equipment should be professionally cleaned and inspected at least once per year at minimum. This allows an experienced service technician a chance to thoroughly clean and sanitize the unit as well as an opportunity to look for and defect items that may have been overlooked during earlier self-performed inspections.
Benefits:
Extended life and use of the equipment assures reliable production at the times when it is needed most. High quality ice, and most important, lower operating cost by maintaining maximum efficiency and operation of the refrigeration, electrical and water circuit components. Multi-Flow can provide a scheduled Preventative Maintenance Program for Ice Machines and may be customized for other equipment you may wish covered in a program. Although your up-front cost may seem a bit higher the benefits and additional life expectancy of the equipment receiving regular maintenance, more than makes up for the cost of your maintenance program.